At Metal’s, we process stainless steel to create assemblies, semi-finished products, machine parts, and large-scale machinery for various markets. Above all, we offer a service that covers the entire logistics process, because we have chosen not to be mere suppliers to our clients, but specialized partners in delivering highly advanced technological solutions.
In this article, we share our approach, production process, the markets and regions we serve, and the values that inspire our work every single day.
From procurement to delivery: we manage and coordinate the entire supply chain
At Metal’s, we simplify our clients’ procurement processes. We handle every aspect - from the initial consultancy and design phase to the delivery of parts to their facilities - because we can control and manage the entire supply chain. Our service includes:
- Technical consultancy and design – We assess project feasibility and propose improvements.
- Engineering – We optimize the project to reduce costs and improve performance.
- Selection and purchase of raw materials – Our clients can suggest their trusted suppliers, or they can rely on Metal’s for the selection. We coordinate all involved companies, timelines, and deliveries.
- Production process – We manage the entire production cycle to meet the specific needs of companies operating in different sectors, from medical to food processing and packaging.
- Quality control – Quality checks cover every stage of the process, including performance, dimensional, and aesthetic inspections, based on the parameters and customizations agreed with each client.
- Worldwide shipping – We can fully manage logistics and handling: we store goods in our warehouses - even large items - provide customized packaging, and deliver the orders directly to the customer’s site, in Italy or abroad. Metal’s also takes care of all bureaucratic and customs procedures.
In doing so, we can act as the sole point of contact for the entire project, optimizing lead times, maximizing production, and allowing our clients to focus on their core business.
Thanks to this integrated approach, over the years we’ve developed increasingly specialized skills and expertise across different industries and markets. This is how we offer tailor-made solutions for each client.
Covered territories: today from Europe to New Zealand, tomorrow the United States
We are constantly seeking new markets to serve. We are working to strengthen our presence in Europe - where our long-standing clients are located - and to expand our services beyond European borders. For example, today, the geographically farthest Metal’s customer is in New Zealand.
In 2024, we began initial assessments to extend Metal’s offering to the United States as well. This is a market we had already served back in 2008, through a collaboration with another Italian company, by manufacturing appliance parts that we shipped directly from our facility to General Electric in the U.S. We are currently evaluating the competitiveness of our products delivered to customers in North America.
This growth opportunity drives us to further optimize our processes and strengthen Metal’s production capacity.
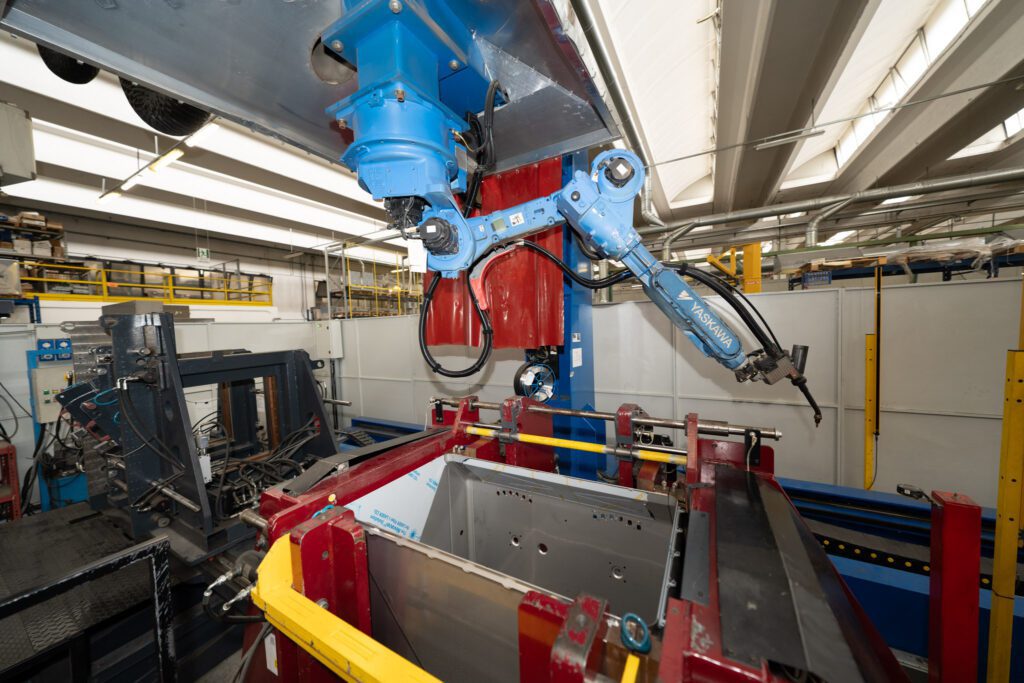
Our production process: technology and organisation
We manage our production process with meticulous attention and flexibility, coordinating all involved parties to ensure high quality standards at every stage and to guarantee on-time deliveries while eliminating waste and delays. Ours is a lean manufacturing system, designed to deliver maximum efficiency and reliability.
Metal’s production process is fully automated and includes various operations: in addition to multiple sheet metal processing systems, we have dedicated areas for milling, welding, both robotic and manual surface treatments, and a large area for assembly.
High energy-saving laser cutting and combined laser punching
Laser cutting is one of the first operations we perform and represents the most advanced technology in steel processing. At Metal’s, we chose to invest in this method by selecting systems with low environmental impact and high energy efficiency. This allows us to maximize production and reduce consumption without compromising quality.
We can produce deep draws up to 20 mm, threading, and, in some cases, bending, thanks to systems that combine laser cutting with punching technologies. This process runs 24/7 with numerical control and features a turret with 59 tools (including 2 multi-tools), entirely managed by our technical department.
One of the most important technologies we have invested in is the MITSUBISHI 8 kW fiber laser cutting system with 3000×1500 mm tables and a cutting capacity of up to 20 mm stainless steel, equipped with automatic loading and unloading. This allows us to process steel in a variety of thicknesses. The system includes a tower with 12 drawers for automatic feeding, featuring fully automated part picking and sorting technology.
This greatly simplifies the production process and allows for a smooth and consistent production flow, with minimal human intervention, within the expected logistics timeframes.
High-precision bending
High-precision steel bending is a key process in the production of semi-finished products and assemblies, as it gives shape to a flat steel sheet without altering its mechanical properties.
It can be performed on various types of steel - including stainless steel, carbon steel, and low- or high-alloy steels - to adapt the product to the requirements of different markets, including the food and medical sectors. For bending operations, we use synchronized CNC-controlled automatic machines, enabling us to produce complex items with heights up to 200 mm, maximum lengths of 2500 mm, and thicknesses up to 2.5 mm.
Stamping with hydraulic presses
During the stamping phase, we use hydraulic presses with a pressure capacity of up to 1000 tons and mechanical presses up to 400 tons. Together with the customer, we design customized molds to optimize costs. Whether hot or cold, stainless steel stamping can be used to produce semi-finished products and assemblies for various industries, such as food, automotive, petrochemical, and chemical sectors.
Automated and certified welding
Our automated welding process is certified according to ISO 3834-2. This certification confirms the implementation of structured welding procedures that comply with international standards and are managed by skilled personnel capable of delivering high-quality welds.
We have introduced fiber laser welding machines into our production departments: an effective alternative to more traditional welding methods such as MIG and TIG. This technology speeds up production, ensures a clean and aesthetically refined product, and minimizes both pre- and post-welding operations.
Cutting-edge milling
Milling enables the precise machining of machine parts and mechanical components. Metal’s facility includes 4.5-meter mobile column milling machines equipped with a rotary-sliding table measuring 2500×2500 mm, with a load capacity of up to 15 tons and top tables of 2000×2500 mm. These state-of-the-art machines allow us to perform CNC drilling and boring operations with the highest level of precision.
Brushing, also with robotic systems
Stainless steel brushing is a highly requested surface treatment in the production of complex assemblies and semi-finished products. It is carried out after bending and welding to remove imperfections and to make the steel smoother to the touch and give it a matte finish.
Brushing serves not only an aesthetic purpose but also a hygienic one: it makes the surface easier to clean and suitable for applications in the food and medical sectors. Our facility is equipped with 3 robotic systems that allow us to continuously perform high-quality deburring, brushing, and polishing.
Assembly of semi-finished products and complex assemblies
Assembly is one of the final stages of our industrial process. Here, we carry out the assembly of parts, finishing operations, and final inspections. Metal’s has a 5,000 m² area dedicated to this activity.
Design and manufacturing of molds
We have an entire department dedicated to the design and construction of equipment and molds, which allows us to produce the necessary tooling for production more efficiently. The department is also equipped with machines for turning, milling, drilling, and grinding. For the design phase, we use Solid Edge software combined with the most modern CAM software for CNC machines.
Quality control at every stage of the process
Ensuring flawless products and improving our services every day is no easy task, but it is essential. For this reason, we carry out strict quality checks at every stage of production. At the end of the process, the semi-finished product undergoes thorough inspection to ensure it meets the standards agreed upon with the client.
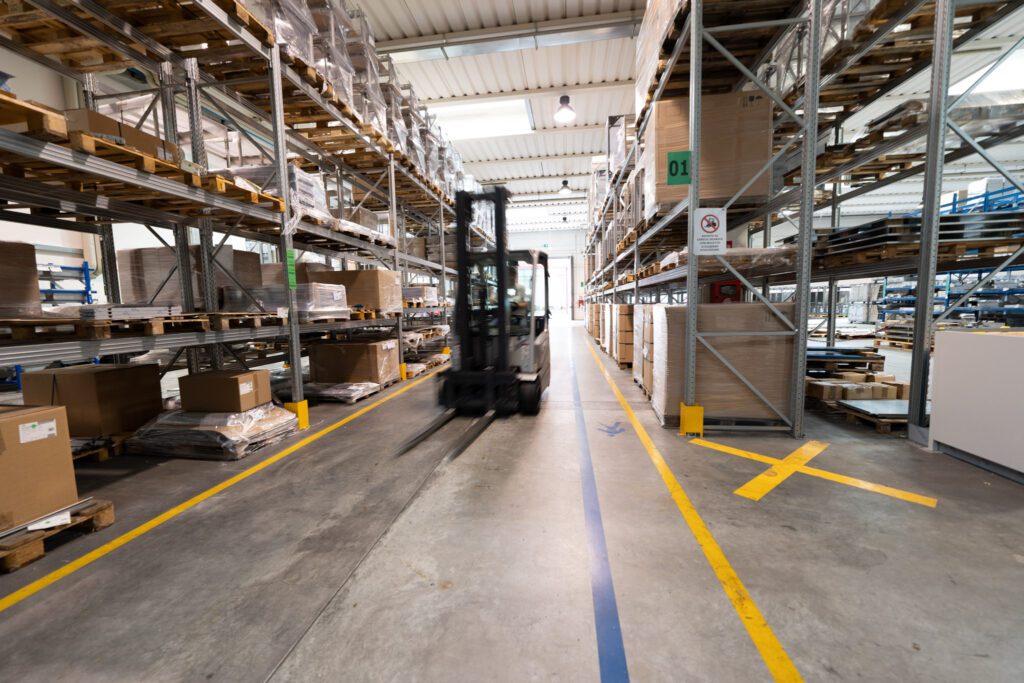
Our machinery and expert technicians
We are able to carry out extremely complex operations in record time, thanks also to our fleet of machinery, which includes, among others: laser cutting systems, bending machines, robotic systems, and milling machines – all selected for their cutting-edge technology and high precision. State-of-the-art solutions, operating continuously (24 hours a day, 7 days a week), managed by our expert technicians who are constantly up to date with the latest innovations. In this regard, we have created a dedicated team of welders tasked with developing new construction technologies and solutions specifically for laser welding, as it allows for excellent results in terms of both cost and performance. Metal's welders are certified according to the UNI EN ISO 9606-1:2017 standard and meet the requirements of the most recent regulations.
The result of our work: assemblies, parts, stainless steel semi-finished products, and large machinery for various sectors
We have been working with and assembling stainless steel for almost 40 years, manufacturing complex assemblies, machine parts, semi-finished products, and components for well-established medium and large-sized companies operating in various sectors, both in Italy and internationally. In recent years, we have also introduced a new addition to our offering: the production of large machinery.
Complex assemblies and machine parts made of stainless steel
We assemble stainless steel with different types of components (such as glass parts, plastics, wiring harnesses) to achieve complex assemblies in advanced stage of assembly. For example, we manufacture devices for the packaging, bottling, medical and pharma sectors.
Semi-finished products and components in stainless steel
We also produce semi-finished products and stainless steel components used in various fields. For example, our work includes accessories for large professional kitchens, stainless steel parts for the bakery market, products for meat processing, refrigeration and the ice cream industry. In addition, we design and create elements for professional dishwashers, switchboards and cabinets, and products for the pharmaceutical and medical sectors.
A mechanical division dedicated to large-scale machinery
In recent years, we have invested in the creation of a new Metal’s division dedicated to the production of large-scale machinery for the packaging, hospital and pharmaceutical sectors, as well as for food processing (packaging, meat and food handling).
In this division, we manufacture complex, large-volume machines using technologies such as milling, TIG, MIG, and laser welding, and automated systems for machine brushing.
This represents an exciting opportunity that we offer both to our European customers and to potential new clients outside Europe.
How we work: our philosophy, our method
At Metal’s, we turn problems into solutions. This is our business philosophy, and to make it a reality, we provide our clients with the expertis e of technicians, engineers, and skilled workers who oversee every phase of the process, from cost evaluation and project feasibility to the creation of a perfect final product. Once completed, all products undergo thorough quality control tests with the primary goal of meeting the targets set by our clients. This is the only way we can deliver assemblies, semi-finished products, and parts of the highest quality, in terms of both performance and design, while fully respecting the parameters and any custom requirements of the project.
As mentioned, we don’t just receive an order, issue a quote, and proceed with production. At Metal’s, we adopt a proactive, consultative approach that supports the entire process, from prototyping to logistics.
Metal’s consulting: improvement proposals starting from the design phase
During the design phase, our technical department assesses the technical feasibility of the project, suggests improvements, and, in the case of critical issues, proposes all viable solutions.
This is what happened, for instance, when a major client in the food & beverage sector asked us to optimize costs while maintaining the product's aesthetics to suit different markets. Similarly, we advised a client in the food processing industry to optimize production by adopting an alternative fastening system to the one previously used: a solution that helped reduce errors, waste, and processing costs.
To further optimize the process, we simulate the final product outcome and create functional prototypes. Once approved, we quickly proceed with production and distribution.
Quality at every stage: from material selection to production
At every stage of the production cycle, from raw material inspection to final product finishing, we ensure compliance with our strict quality standards. This allows us to meet every request with flexibility and reliability, both in the markets we already serve and in new sectors. We source our stainless steel from suppliers that meet high quality standards, and for components made of other materials, we either coordinate with our clients’ suppliers or assist in finding partners who fulfill all necessary requirements.
We are partners, not just suppliers
Being a partner means, above all, stepping in when our clients are facing difficulties.
For instance, it may happen that they don’t know who to turn to for a specific supply, or that their usual supplier is suddenly unable to deliver. That’s exactly what happened during the Covid-19 pandemic, when a client in the food processing sector suddenly found themselves without a crucial component because their trusted supplier had halted operations due to lockdown restrictions. We quickly identified an alternative supplier, allowing them to continue production without interruption. At the same time, being a partner also means listening to our clients' needs and proposing even more efficient solutions. That was the case when we suggested a key change in the production process to a long-standing customer in the food industry. The goal: to cut costs and lead times by introducing an automated process. Or when we proposed technical improvements to two food processing clients, significantly boosting the performance of a product we had been manufacturing for them for years.
Metal’s people and the Academy: at the heart of our work
Last but not least, the people. Those who work at Metal’s are prepared, motivated, energetic. Qualities that determine the quality of work, enrich the relationship with our customers and characterize our company on the market. This is why continuous training is essential for us and from 2022 we have an in-house Metal’s Academy to train new resources.
What is Metal’s Academy? It’s a training program designed for those who want to become part of our world. It gives new hires, in specific roles, the opportunity to follow a complete training path before entering the production departments. The program combines theoretical and practical learning, focusing on the most critical and complex technologies used within the company.
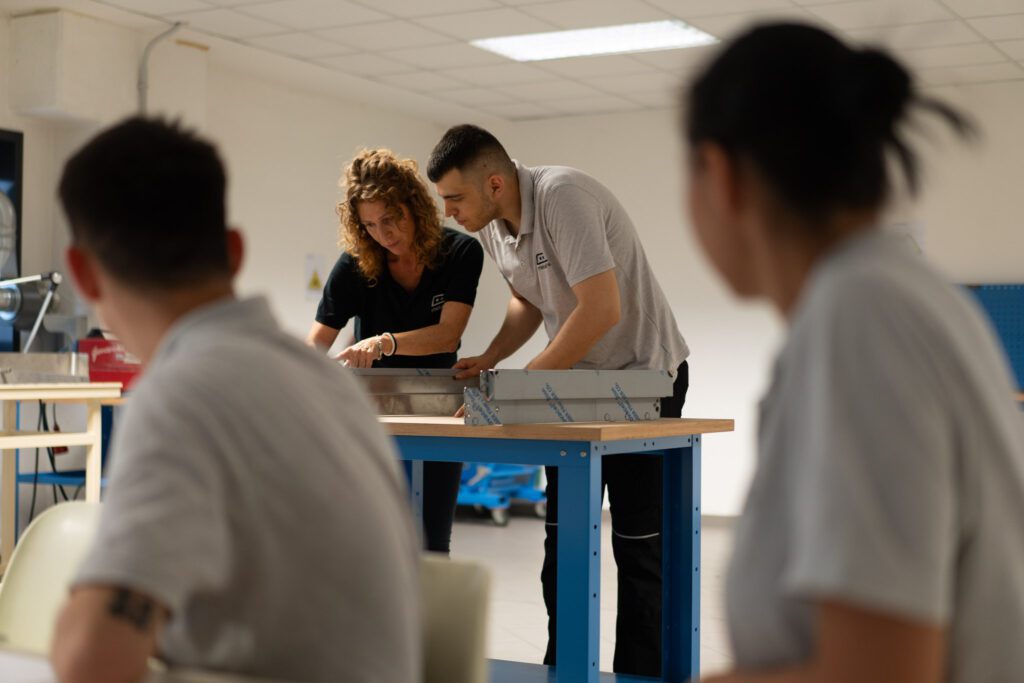
Our certifications: a guarantee of safety, quality and sustainability
At Metal’s, we are committed to advanced policies in quality, safety, and sustainability. We have obtained international certifications such as ISO 9001:2015 for our management system, ISO 45001:2018 for occupational health and safety practices, and ISO 14001:2015 for our environmental management system. As previously mentioned, Metal’s welders are certified according to UNI EN ISO 9606-1:2017 and comply with the most up-to-date regulatory requirements. Furthermore, the quality of our welding processes is certified under UNI EN ISO 3834-2:2021.
For several years now, we have also adopted a company-wide “Green Mission” to guide our choices and investments with a focus on sustainability. This has led to important achievements, such as increasing green energy production, reducing waste, and cutting CO₂ emissions. We installed a photovoltaic system that has brought us close to total energy self-sufficiency. Combined with our in-house nitrogen generator, it ensures stability in gas production costs, which is essential for powering our cutting systems. This investment is vital not only for energy security but also for reducing road transport and related emissions.
Our most recent and exciting milestone has been measuring our carbon footprint. Over the coming months, we’ll be working on our sustainability plan, with the goal of publishing Metal’s first Sustainability Report in 2026.
Would you like to get in touch with us?
At Metal’s, we carefully select the clients we work with - medium to large-sized companies - and support them throughout every stage of the logistics flow: from concept to the creation of stainless steel assemblies, semi-finished products, and machine parts. Would you like to learn more?