At Metal’s, we have enhanced our machinery fleet with robots and new equipment capable of efficiently managing the automation of finishing processes on large semi-finished components.
By doing so, we provide our customers with an increasingly complete service and product, centralizing and automating operations while reducing reliance on external partners. The advantage? Optimized time and costs, along with in-house processing that adheres to our high-quality standards.
In this article, we will explore why we chose to automate finishing processes, the technologies we have adopted, their benefits, and the key challenges for the future.
Why we chose automation for finishing large machine parts
Finishing processes on stainless steel are essential for meeting specific technical and aesthetic standards. They allow for precise removal of irregularities, oxidation, and the achievement of the desired visual appearance.
However, when these processes are required for large semi-finished components, challenges arise. We are dealing with parts that exceed 1,000 kg or have thicknesses ranging from 5-6 mm up to 2.5 cm, requiring specialized technologies to maintain quality and reduce the physical burden on manual operators. Treating the surfaces of such large and thick components—often intended for the food or packaging industries—can be highly demanding for workers, making it a potential "weak link" in the production chain. This is why we decided to invest in robotics.
For large-scale components, robots leverage industrial technology to replicate manual brushing finishes. When properly programmed by a Metal’s operator, this system becomes a key asset, ensuring high-quality standards and consistent execution times. In the mechanical department, we have developed a customized robotic workstation specifically for large components. Unlike the robotic cells implemented in our other departments - where we process hundreds of pieces at a time - for this division, we designed a tailored area in collaboration with Metal’s technical department. Since we work with limited quantities, often one piece at a time, we adapted the cell to the product, standardizing the workstation to ensure versatility and adaptability in handling parts of different sizes and heights. The result? Improved cost efficiency, optimized processing times, and a more streamlined workflow.
The advantages of robots for these processes
Automating the finishing of large components enhances the overall production workflow, enabling efficient brushing and standardized finishes. Additionally, it provides customers with:
- Consistent aesthetic quality
- Reliability in production times and results
- Guaranteed and scheduled processing times
Precision and attention to detail, even for small batches
Large semi-finished components are complex structures—not only in terms of size and weight but also in the type of processing required. They are often used in food processing, packaging, and the pharmaceutical industry, where they handle significant production volumes. Manufacturing a single piece can sometimes take up to a month. Thanks to automation, at Metal’s, we can efficiently produce even small batches while maintaining high standards. This allows us to build one machine at a time with exceptional precision and attention to detail.
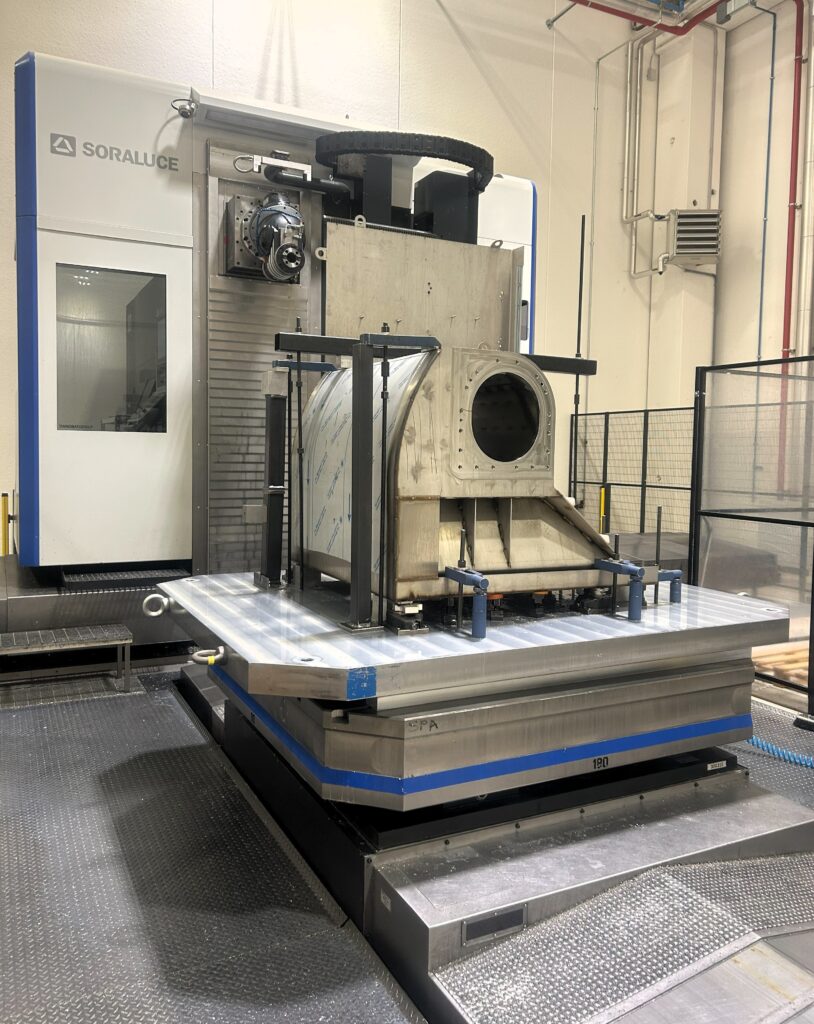
A new milling center for large machine parts processing
To continuously enhance our services and add greater value to large components, we have expanded our machinery fleet with a new milling center.
Equipped with advanced mechatronic technologies, this specialized system allows us to perform flattening, boring, threading, reaming, and final measurement in a single phase, eliminating the need for multiple repositioning steps. Thanks to its dual rotary table, positioning and clamping operations can be carried out in masked time while the system continues working on the second table.
The system also features a specialized probing software that detects deviations in the raw component and corrects them at the source, significantly reducing setup time. With this new milling center, we can manage the entire production process in-house, maintaining our high standards without relying on external suppliers. This enables us to efficiently plan operations, provide our customers with cost and lead-time certainty, and significantly increase our flexibility in meeting delivery schedules.
Looking to the future: new markets and opportunities
The stainless steel processing industry is fast-paced and constantly evolving. Thanks to the innovations we have implemented—including new technologies and our dedicated mechanical division for large machinery production—we continue to move forward, striving to offer our customers the most complete product possible.
Beyond our ongoing commitment to sustainability, we are also focused on expanding into new markets. We are currently exploring international opportunities, including a potential entry into the U.S. market. Over the coming months, we will carefully assess our target audience, the competitiveness of our products, market opportunities, and potential challenges—such as customs and logistics—to lay the foundation for new and exciting collaborations.
Do you want to know more?
Do you need large semi-finished components? Discover why you should trust our professionals. Ask for our consultation and evaluate the benefits you can gain from our expertise in your processing needs.