Metal’s, oltre la lavorazione dell’acciaio inox: un servizio che copre l’intero processo logistico
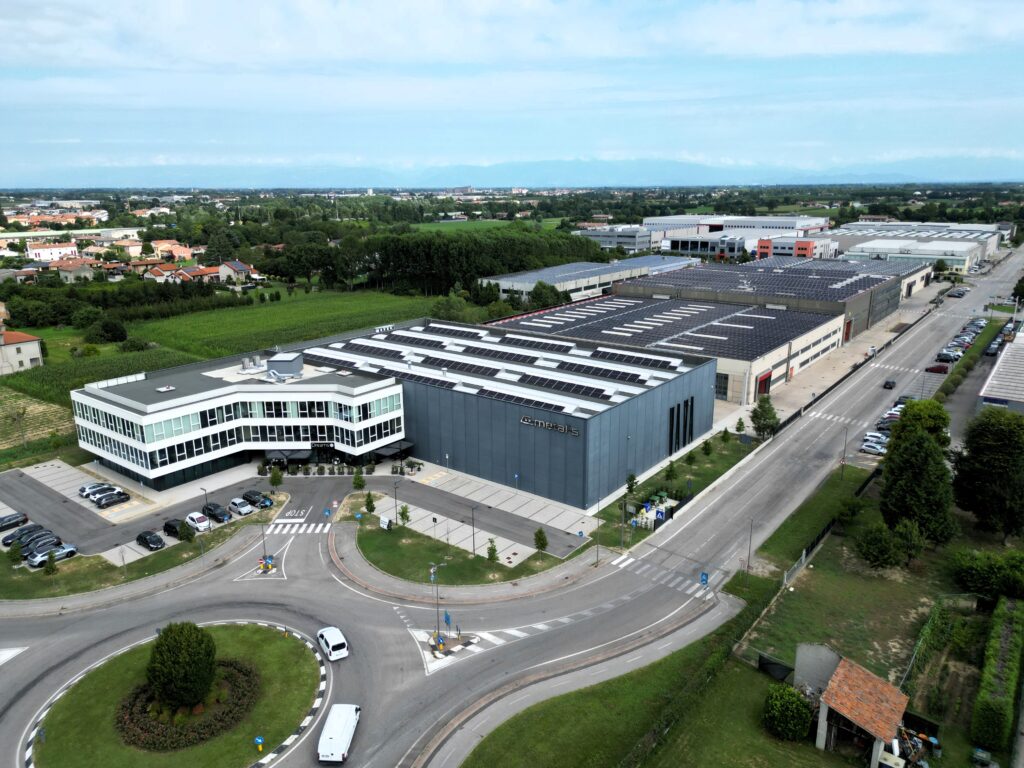
In Metal’s lavoriamo l’acciaio inox per realizzare assiemi, semilavorati, parti di macchine e grandi macchinari destinati a diversi mercati. Soprattutto, forniamo un servizio che copre l’intero processo logistico, perché abbiamo scelto di non essere semplici fornitori per i nostri clienti, ma un partner specializzato nella realizzazione di soluzioni tecnologicamente elevatissime. In questo articolo, ti raccontiamo […]
Automatizzazioni delle finiture su parti di macchine di grandi dimensioni: l’esempio Metal’s
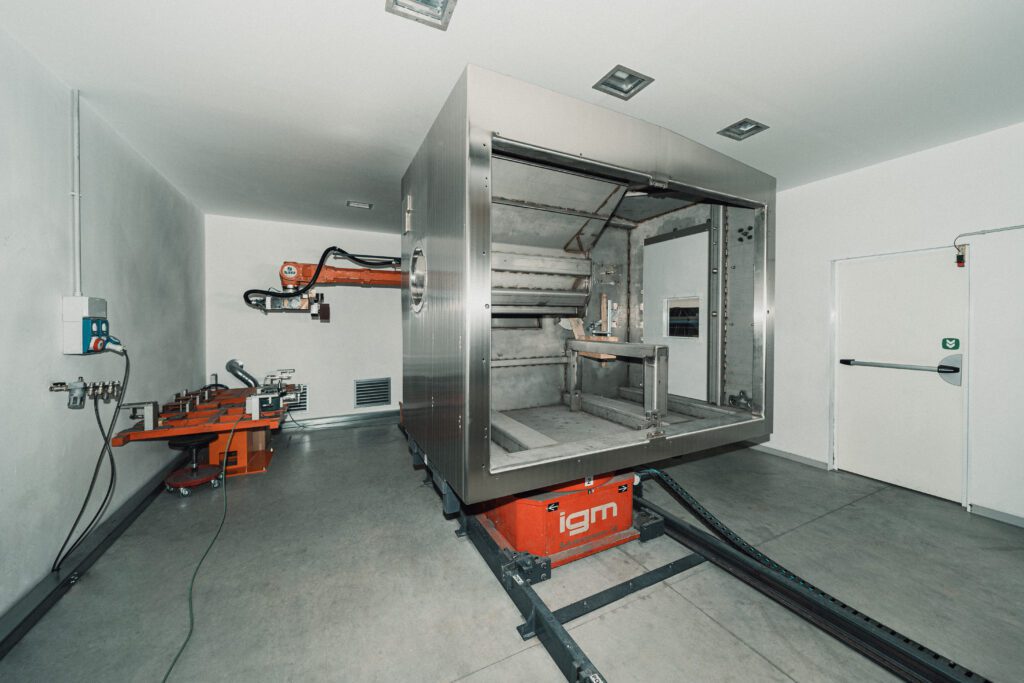
In Metal’s abbiamo implementato il nostro parco macchine con robot e nuovi macchinari capaci di gestire al meglio le automatizzazioni delle finiture su semilavorati di grandi dimensioni. Così facendo, possiamo fornire ai nostri clienti un servizio e un prodotto sempre più completi, centralizzando e automatizzando le lavorazioni e limitando le collaborazioni con partner esterni. Il […]
Saremo presenti a IFFA 2025: la fiera leader mondiale per l’industria della carne e delle proteine
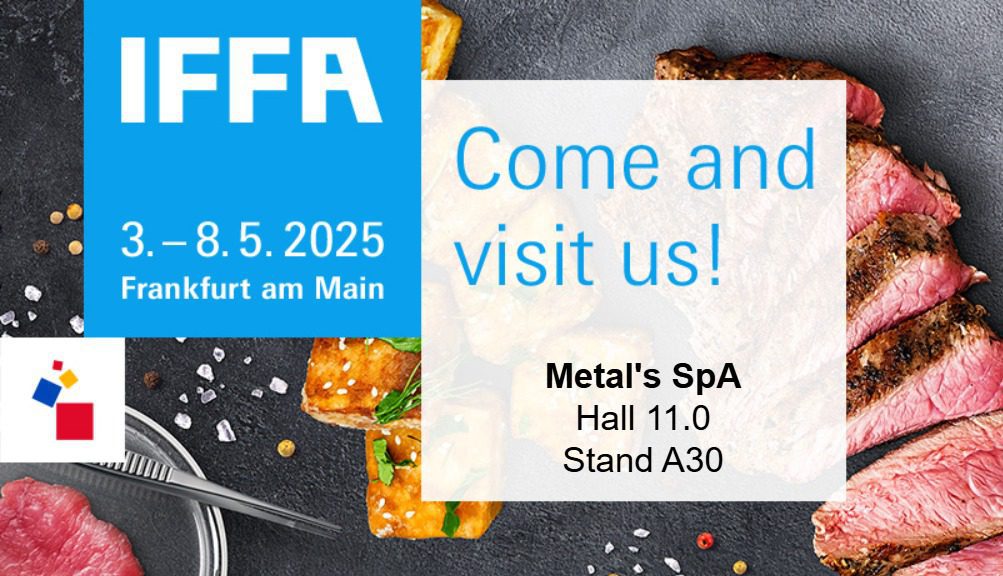
Siamo lieti di annunciare che parteciperemo come espositori a IFFA Frankfurt 2025, l’evento internazionale di riferimento per l’intera filiera della lavorazione e trasformazione delle carni e delle proteine, in programma dal 3 all’8 maggio 2025 presso il centro fieristico di Francoforte. 📍 Ci trovate allo Stand A30 | Hall 11.0 La nostra presenza a IFFA […]
Dadi in gabbia e altre modifiche per ottimizzare la produzione a costi certi: una case history Metal’s
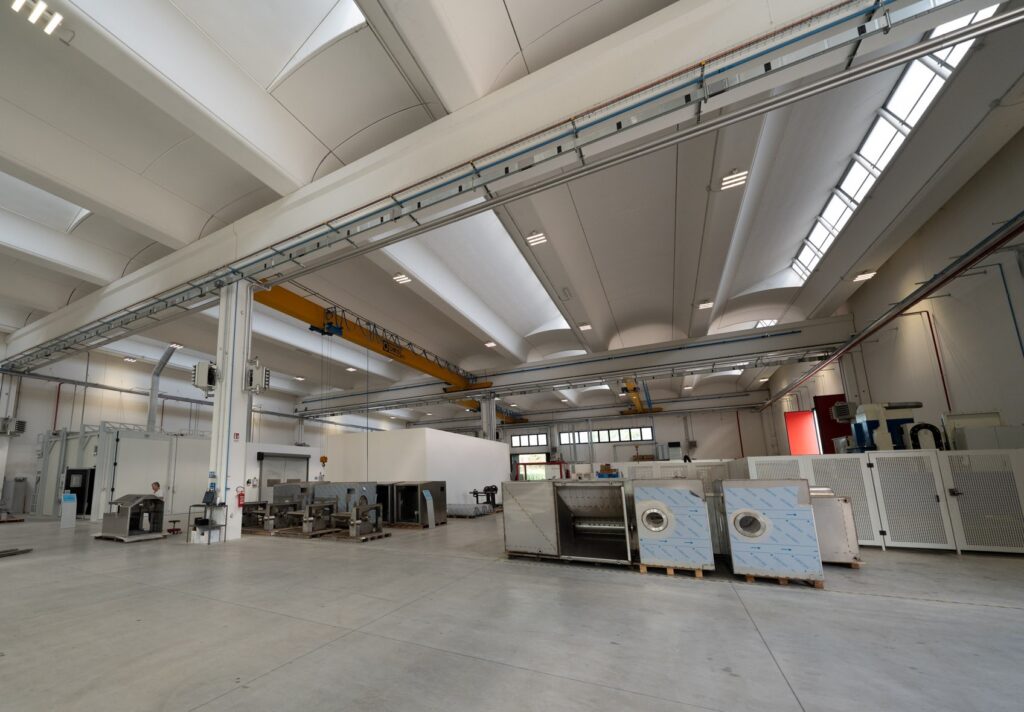
In Metal’s possiamo migliorare il progetto di un semilavorato o di un assieme complesso per ottimizzare la produzione a costi certi. Trovare soluzioni adeguate alle esigenze dei committenti, consigliando loro miglioramenti specifici, consente di ridurre la marginalità di errore e realizzare prodotti di alto livello, già pronti all’uso o da assemblare. In Metal’s il nostro […]
La piegatura dell’acciaio: una lavorazione ad alta precisione
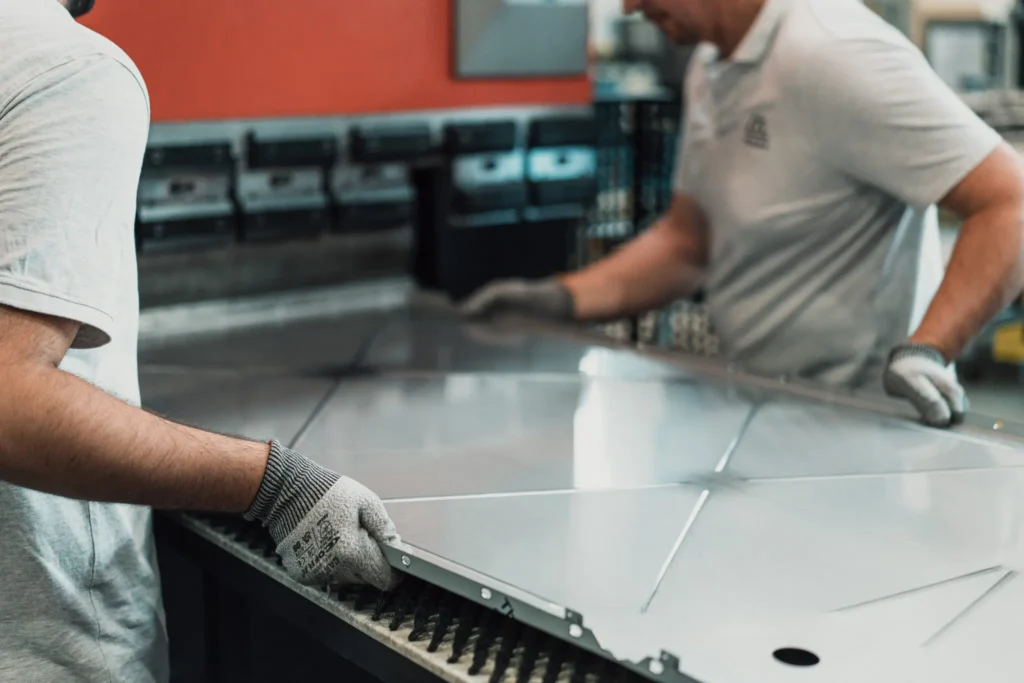
La piegatura dell’acciaio è un processo chiave nell’ambito della produzione di semilavorati e assiemi perché consente di attribuire una forma – anche complessa – a una lastra di acciaio piatto, senza alterarne le proprietà meccaniche. In questo articolo vedremo meglio di cosa si tratta, le sue caratteristiche, i vantaggi, le diverse tipologie di piegatura e i macchinari […]
Metal’s per gli assiemi complessi: la fornitura di sistemi in avanzato stato di assemblaggio
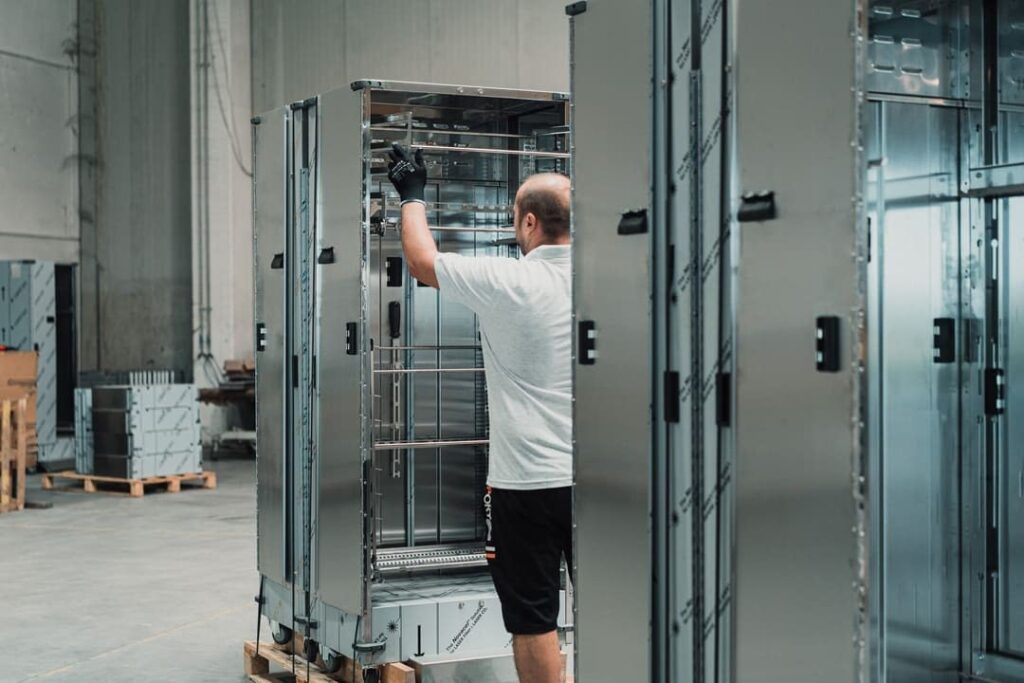
Quando il nostro ufficio commerciale riceve una commessa per la realizzazione di un assieme complesso, la macchina di Metal’s si mette in moto per rispettare le richieste e le tempistiche concordate con i nostri clienti. Come funziona questo processo, quali parti coinvolge attivamente e quali sono i vantaggi per chi si rivolge a noi? L’acquisto […]
Case history Metal’s: modifiche tecniche per migliorare le performance di un progetto
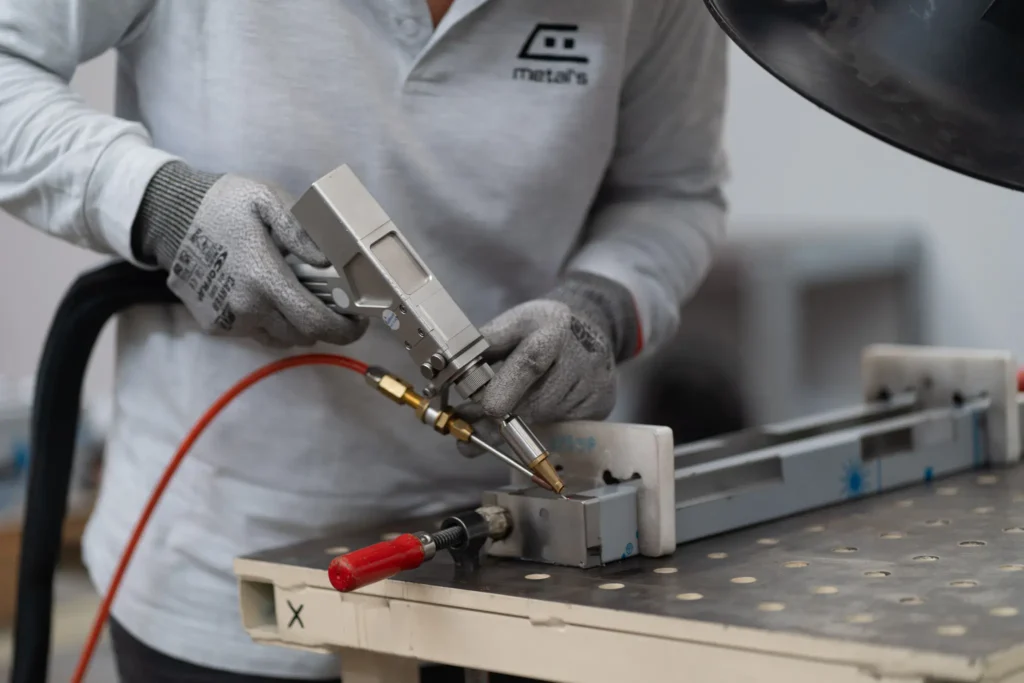
Alcune modifiche tecniche su un progetto già concordato e avviato da tempo possono migliorare la qualità di un assieme o un semilavorato a livello funzionale, estetico e, non da ultimo, economico. Cambiamenti che coincidono spesso con l’arrivo di nuove tecnologie, sempre più all’avanguardia e performanti. Quando il parco macchine di Metal’s si arricchisce di una nuova apparecchiatura funzionale al progetto, il nostro ufficio tecnico valuta eventuali implementazioni al […]
Deformazione mediante stampaggio dell’acciaio inox: cos’è e come impiegarlo nelle proprie realizzazioni
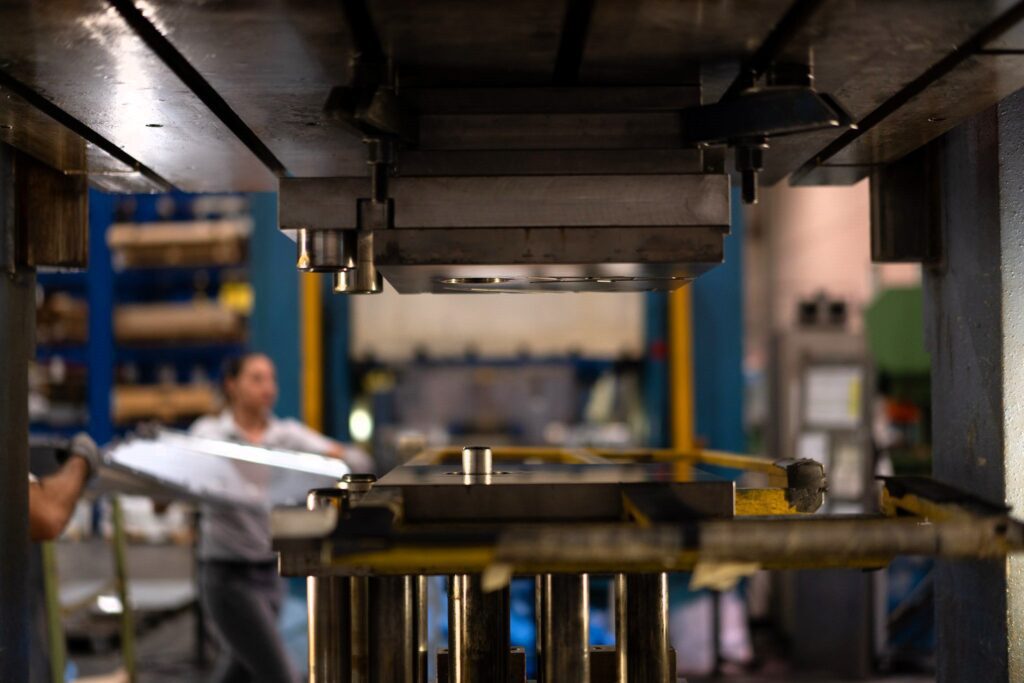
Lo stampaggio dell’acciaio inox è una lavorazione che consente di dare una forma particolare al metallo. Si possono realizzare profili geometrici, anche complessi, senza eccessivi sprechi di materiale, mantenendo invariate tutte le preziose caratteristiche dell’acciaio inossidabile. Per effettuare lo stampaggio servono macchinari all’avanguardia, oltre a una profonda conoscenza del metallo e della sua lavorazione, valutando – caso per caso – […]
Case history Metal’s: saldatura, un processo automatizzato certificato ISO 3834-2
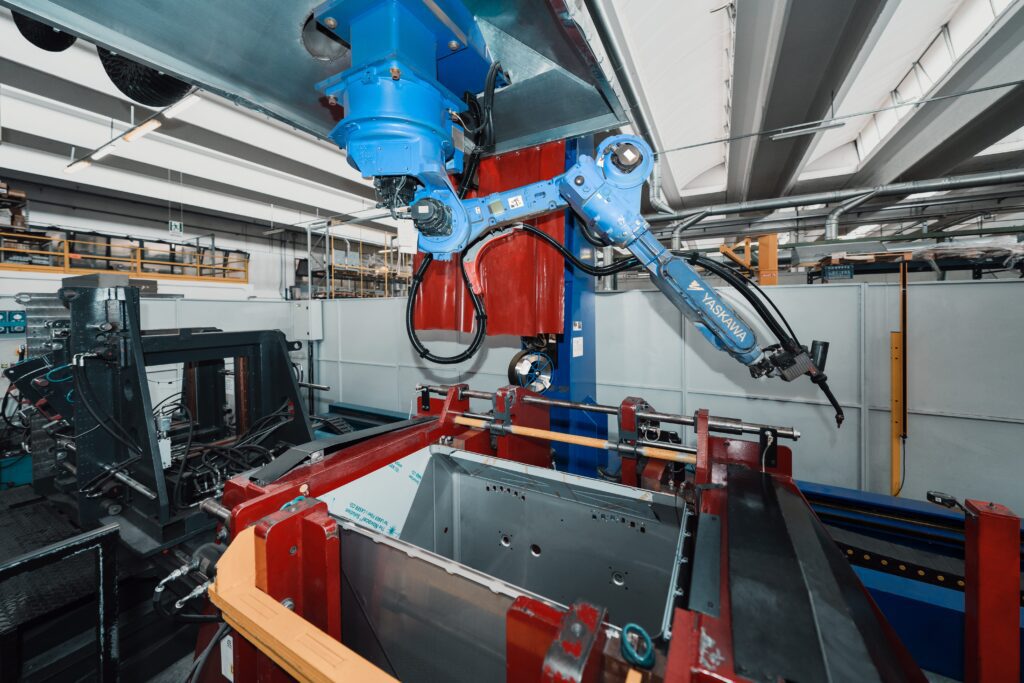
In Metal’s possiamo eseguire commesse con saldatura certificata, per soddisfare le esigenze specifiche dei nostri clienti. Disponiamo, infatti, di un ampio parco macchine, completo di sistemi automatizzati che ci consentono di certificare determinate lavorazioni, oltre a migliorare la produzione e velocizzare le operazioni per rispettare sempre le tempistiche concordate. Ponendoci come unico referente, possiamo curare […]
Diversificazione dei mercati: l’importanza della supply chain
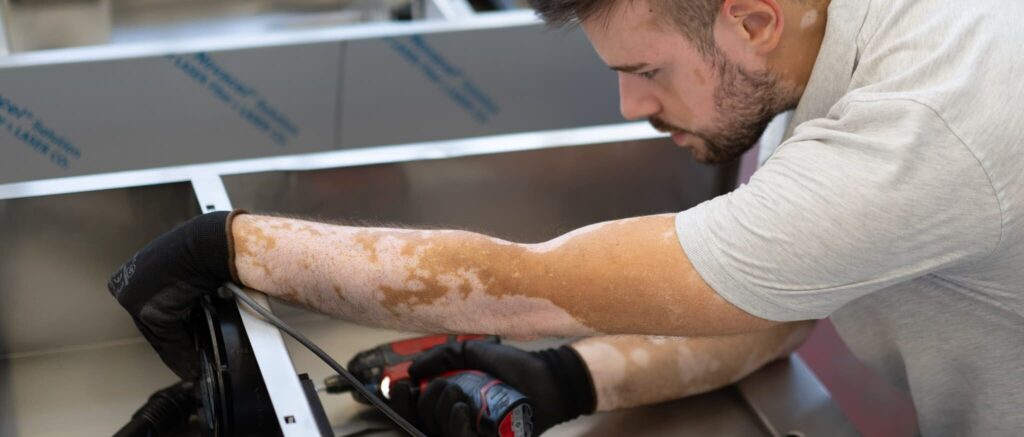
La gestione della supply chain aziendale, per la diversificazione dei mercati e la crescita del business, mira all’ottimizzazione e all’efficienza di tutte le attività, dalla produzione alla logistica. Un processo complesso, dinamico, volto a raggiungere il risultato prefissato e che, fase dopo fase, coinvolge diverse figure professionali, coordinate tra loro per una gestione efficace e […]
Acciaio inox nei manufatti: come aumentarne la durata?
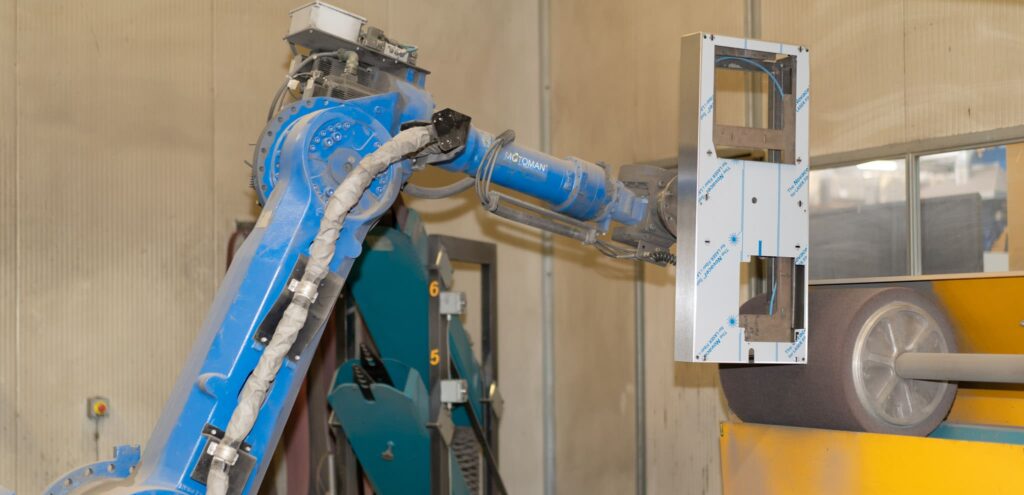
Aumentare la durata dei manufatti e degli assiemi complessi realizzati in acciaio inox è un’opzione importante per chi vuole offrire prodotti di alta qualità, capaci di resistere all’usura e al tempo. L’acciaio, infatti, è composto da una quantità variabile di metalli come il ferro e il carbonio, oltre al nichel e al cromo. Quest’ultimo, in […]
L’impronta ecologica di Metal’s e i prossimi step per l’ambiente
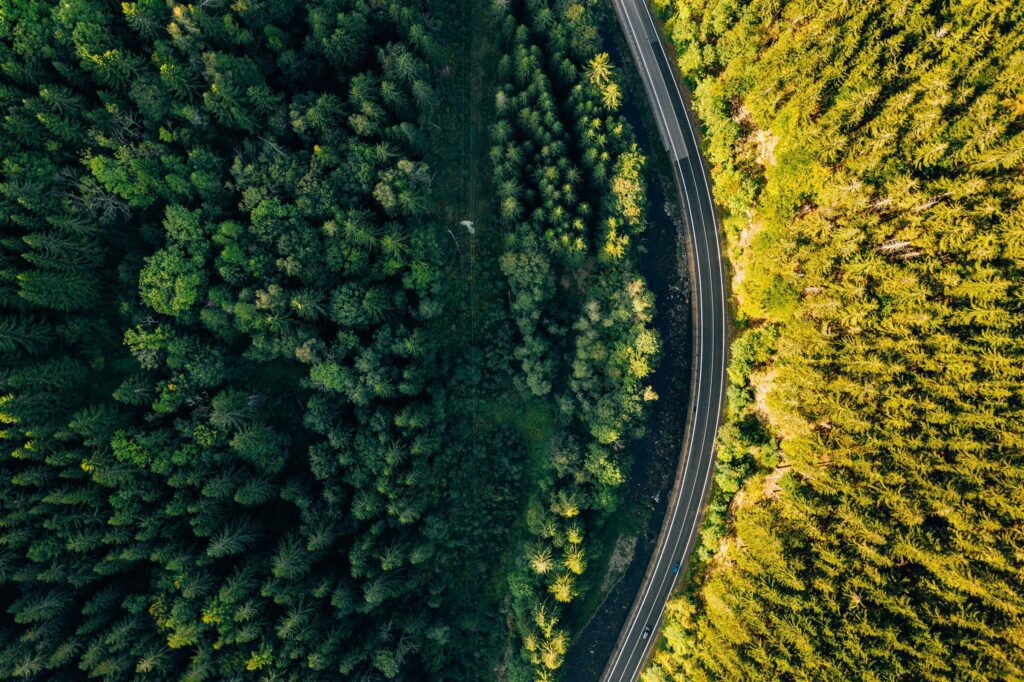
L’ambiente è un tema che ci sta a cuore. Ecco perché nel 2024 in Metal’s abbiamo deciso di ampliare la nostra Green Mission, avviando due nuovi progetti per la sostenibilità: Propositi ambiziosi, che abbiamo delineato in dettaglio nel corso della presentazione del piano biennale per lo sviluppo sostenibile, e che ci serviranno per offrire ai […]
Acciaio inox alimentare: quali tipologie?
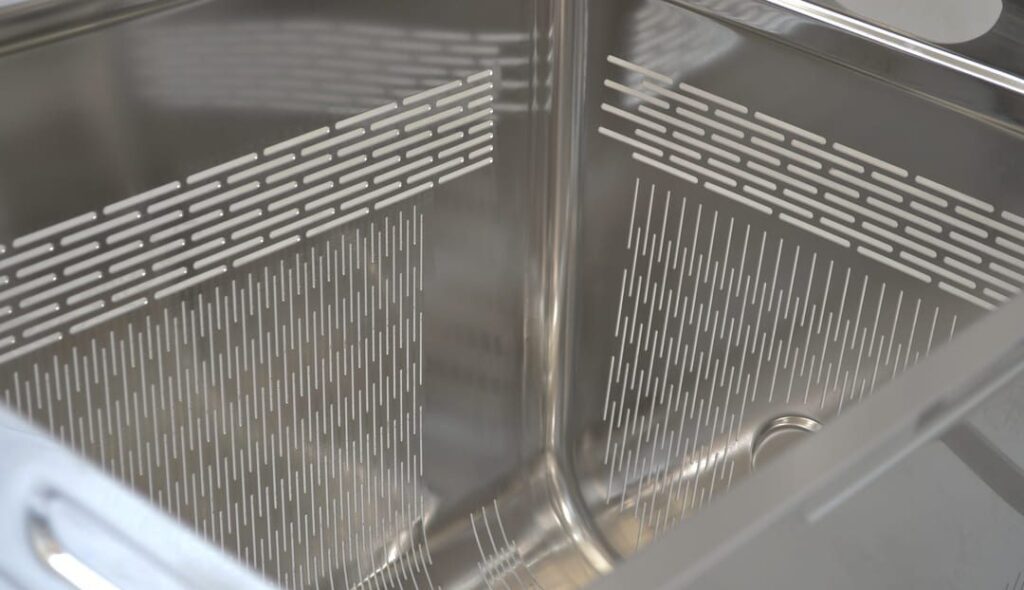
Quando si parla di acciaio inox alimentare si fa riferimento a una particolare lega di acciaio inossidabile utilizzata nell’industria del beverage e food. Viene impiegata soprattutto in questo ambito perché evita le contaminazioni e offre altri importanti vantaggi. Ma quante tipologie di acciaio inox alimentare esistono, quali sono le sue caratteristiche e come si distinguono […]
L’impegno di Metal’s: un piano biennale per lo sviluppo sostenibile
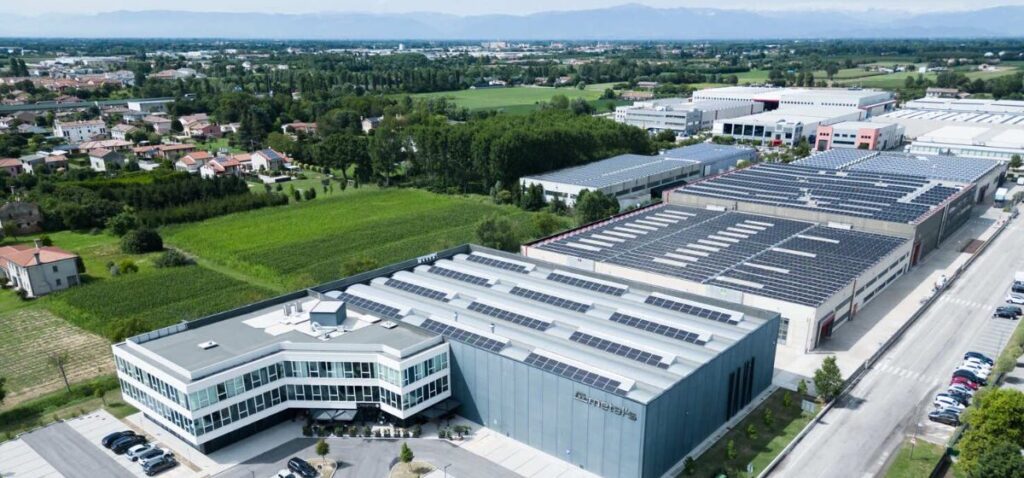
In Metal’s l’impegno per la sostenibilità e l’ambiente è all’ordine del giorno anche per tutto il 2024. Il rispetto per il pianeta – e la comunità in cui operiamo – è una tematica a cui teniamo molto e sono diversi i progetti che intendiamo realizzare per sviluppare ulteriormente la nostra Green Mission. Del resto, negli […]
Case history Metal’s: come abbiamo migliorato la produzione con la lavorazione automatizzata

In Metal’s realizziamo assiemi, semilavorati, parti e componenti in acciaio inox, sia semplici che complessi. Lavoriamo l’acciaio, ma ci occupiamo anche della fase progettuale e tecnica, consigliando ai nostri clienti alcune migliorie per ottimizzare i tempi di lavorazione o ridurre i costi di produzione, ovviamente senza ripercussioni sulla qualità. Il nostro è un lavoro ricco […]
Manca poco ad Internorga!
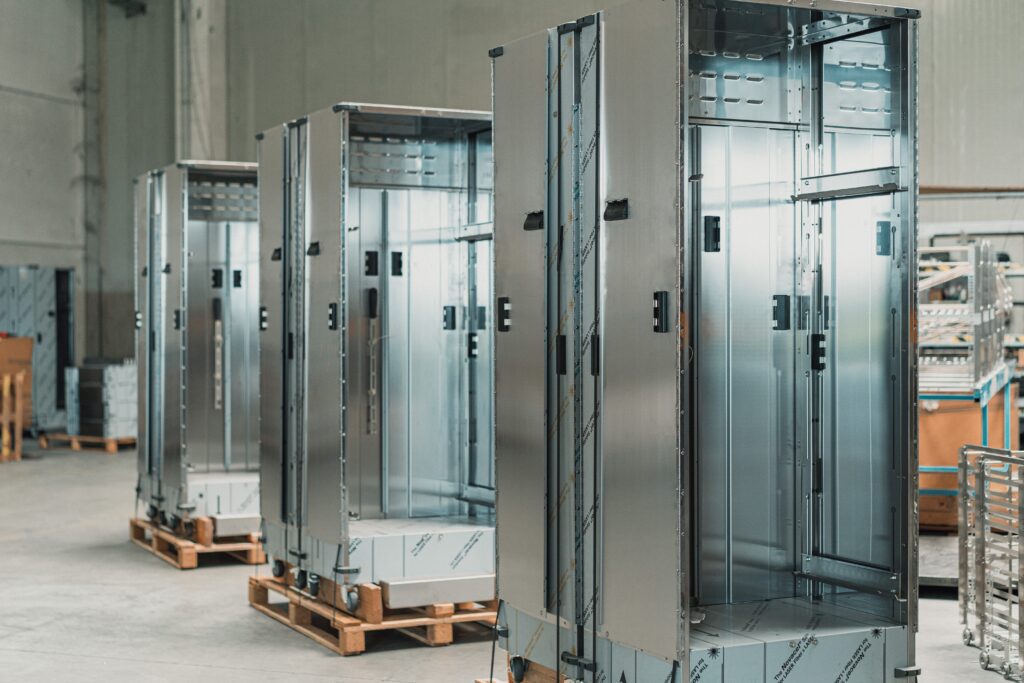
Siamo felici di annunciare che a partire da domani parteciperemo alla Fiera Internazionale Internorga ad Amburgo! Internorga è il punto di incontro per eccellenza del settore dell’ospitalità e del food, riunisce innovatori, esperti e appassionati da tutto il mondo.Dal 8 marzo al 12 marzo, vi aspettiamo presso il Padiglione B7, Stand 516.Sarà un’ottima opportunità per […]
Trattamenti superficiali dell’acciaio: pallinatura e satinatura
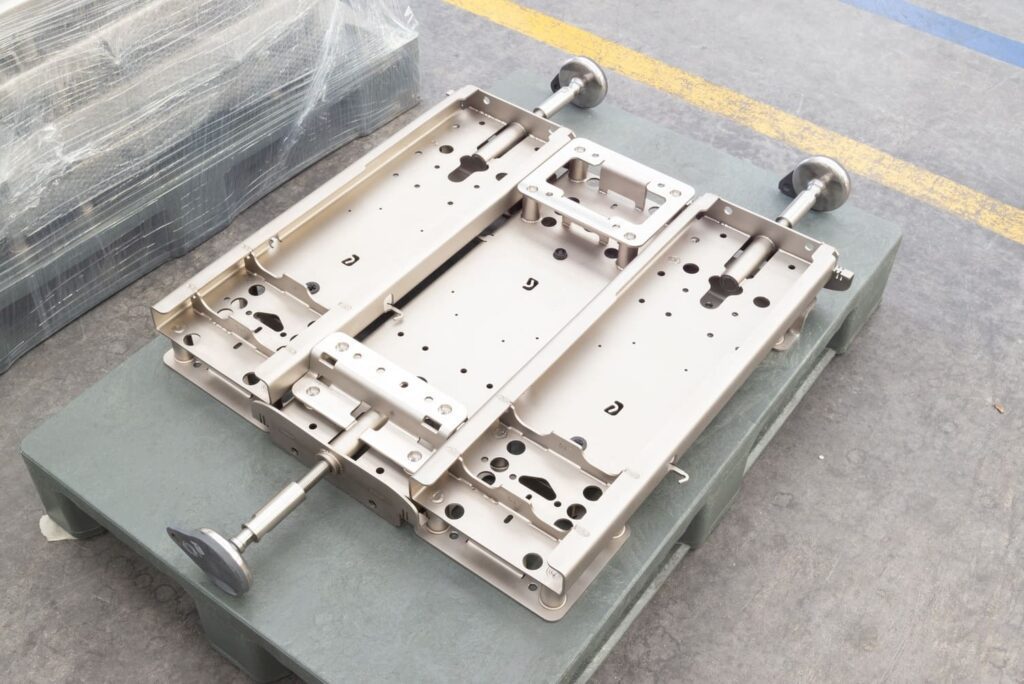
Pallinatura e satinatura sono due tra i trattamenti superficiali dell’acciaio più utilizzati per rifinire le superfici in inox. Ma quali obiettivi consentono di raggiungere e come si differenziano i due processi? In questo articolo vedremo vantaggi, caratteristiche comuni e differenze tra le due metodologie e come utilizzarle al meglio. Cosa sono i trattamenti superficiali dell’acciaio […]
Case history Metal’s: ottimizzare i costi, mantenendo l’estetica del prodotto per adattarlo a diversi mercati
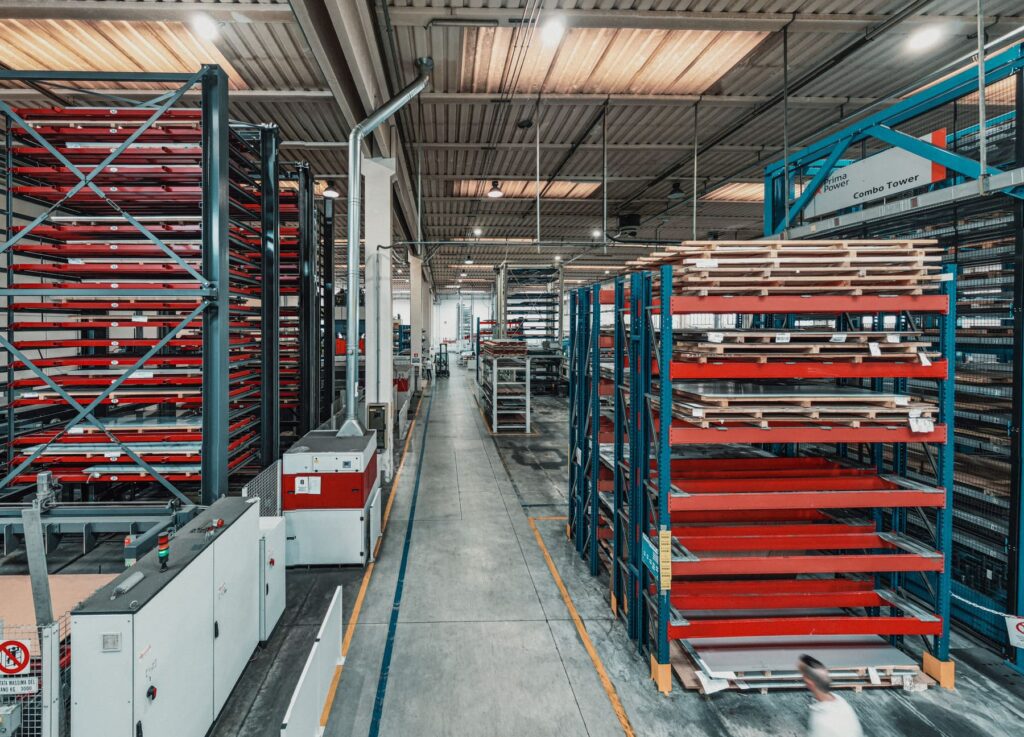
In Metal’s realizziamo assiemi, semilavorati, parti e componenti in acciaio inox nelle quantità concordate, gestendo l’intero processo: dagli ordini fino alla consegna. Possiamo occuparci ogni tipo di progetto, soprattutto quelli più complessi e sfidanti, seguendo ogni fase del processo logistico e produttivo. Il nostro obiettivo è consegnare ai nostri clienti i prodotti richiesti, rispettando le […]